What is Lean Laboratory Management?
Learn more about lean laboratory management in this comprehensive guide. Implementing lean principles in your clinical lab is easy with a proper plan. Free excel template included.
INFO
Brannon Hogue
8/14/20246 min read

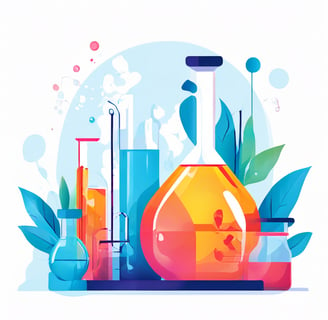
Definition of Lean Laboratory
Lean laboratory management — taking lean manufacturing principles and applying it to the lab work flow, can improve throughput and efficiency in the lab.
The main focus of the lean framework is to drive efficiency through improved cost management and speed. Reaching the next level of cost efficiency is what most labs strive for in the modern economic environment.
Key Goals of Lean Laboratory Management
Improving productivity while driving down cost is a goal for almost all lab supervisors.
It is getting harder, the rise of inflation is taking a toll on lab services, affecting everything from the cost of supplies to labor expenses.[1]
This is a big hurdle, but finding ways to run smoothly and not worry about excessive resource usage is one of the larger questions facing the industry in 2024. Finding a balance between quality, resources, and time is the magic sauce. The more correct name is the “Magic Triangle”. The critical parts of the triangle are as follows:
Quality: The scope and performance of the project deliverables. It refers to how well the end product meets the specified requirements and standards.
Resources (Cost): The budget, people, materials, and other assets required to complete the project.
Time: The schedule or timeline for completing the project, including milestones and deadlines.
First, finding where your labs triangle sits is important before improving it. Finding which metrics you want to track will depend on what type of lab you manage, but declaring and monitoring KPI’s in an excel sheet would be a good start, we have a good article about KPI’s here[2].
We can give you good KPI’s to start tracking each parts of the triangle.
This spreadsheet allows you to track all the key performance indicators (KPIs) mentioned earlier on a month-to-month (MoM) basis throughout the year.
Quality KPIs
Accuracy: % of test results that are correct
Proficiency Testing: Performance on external quality assessments
Complaint Rate: # of customer complaints per 1,000 tests
Resource KPIs
Cost per Test: Average direct cost to perform each test
Supplies Expense: Total spent on reagents and consumables
Staff Productivity: # of tests performed per FTE
Time KPIs
Turnaround Time: % of results delivered within target TAT
Stat TAT: Average time for emergency test results
Uptime: % of time instruments are operational
Getting Started with Lean Laboratory Management
Conduct Value Stream Mapping
A good and low risk place to get started with lean laboratory management is mapping out current processed to identify waste and bottlenecks. A good way to do this is to observe and document each step in the specimen management process from collection to resulting on a piece of paper or a word doc.
From this map, you can create a plan process mapping symbols and notation to create a visual representation of the current state. This may include steps, decision points, delays, inventory, and information flows. Get your staffs input on this map to enrich the overview and get a better and more in-depth understanding of their perspective as well.
When this is done, analyze the current state map to identify the 8 wastes of Lean: Defects, Overproduction, Waiting, Non-utilized Talent, Transportation, Inventory, Motion, and Extra-Processing (DOWNTIME). Focus on eliminating these non-value-added activities.
With this you can plot a future state map of a more ideal workflow, again, do not change all of it just small pieces one at a time.
Implement 5S Workplace Organization[7]
Sort - Go through all items in the lab and sort them into categories: necessary, unnecessary, or needs evaluation. Next, you should remove any unnecessary items that are not used regularly or are obsolete. This will free up valuable space.
Set in order - Arrange necessary items in your workflow in a logical and easy to find manner. Most frequently used stuff should be out and ready for use. Upgrade the workflow with color coding and labels.
Shine - Clean the counters, weekly task lists laminated for expo markers are good for delegation of tasks like these.
Standardize - Develop standard operating procedures (SOPs) for maintaining organization, performing tasks, and using equipment. This ensures that everyone is following best practices consistently.
Sustain - Make 5S a habit and part of the lab's culture. This requires ongoing commitment, communication, and leadership.
Create a Visual Workplace[8]
Things like labels and colors act as clear visual cues for what is going on in the workflow at all times. It can convey workflow changes better as well, which decreases workflow change adaptation time. Again, workspaces can adopt changes faster with more help from visual cues. A change like this also allows for quicker flow assessment and resource availability.
Establish Work Cell Specimen Processing
Work cell specimen processing is a method of organizing laboratory tasks into efficient, self-contained units. First you should determine tools, tasks, materials, and information needed for each workstation. If you are really committed, ensure that all tools and materials are within easy reach to reduce movement and improve efficiency. After, arrange equipment and materials in a logical sequence to follow the workflow. This is another opportunity to add colors and visual cues to reduce error and the time it will take to get used to the new workflow.
By implementing these lean laboratory management practices, labs can drive greater efficiency, productivity, quality, and continuous improvement. The key is to eliminate wasted time and resources while empowering lab personnel to optimize processes for the best results.
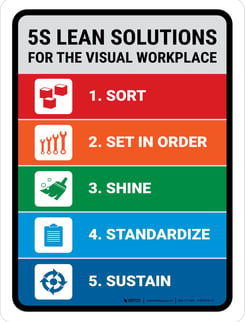
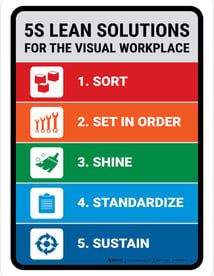
image from creativesafetysupply.com[6]
Benefits of Implementing Lean Laboratory Practices
There are many examples of improvements in the lab that can be measured with something other than less-hair-pulled-out. For example, at a satellite location, analyzing extra tubes collected showed that 87-95% do not get used for testing[4]. This is a huge sink point in the workflow that could be optimized.
Another example, value stream mapping of bone marrow collections found that only 42% of lab tech time was value-added. Improving this process can make for a much better use of skilled labor.
These are just a few but are important to take into account when making the transition to a lean workflow for your lab.
Increased Efficiency and Productivity
Streamlining and really digging deep into your labs SOP’s is the quickest way to improve perfomance in your lab. This may involve reducing assay volumes, eliminating unnecessary steps, or automating manual processes. These small tweaks lead to significantly higher productivity and efficiency, just remember to not change too much at once, because knowing which changes have the most impact is important when tracking performance.
"They’re those pesky hiccups that prevent you from reaching your maximum speed. Much like a deadlifter whose grip strength limits their overall lifting capacity, bottlenecks in one area of your business can cap the efficiency of multiple workflows" a great quote from comidor.com[5]
Fine tuning your labs workflow can lead to reduced lead times and operation costs. All of these tweaks should ultimately manifest through lower levels of work needed to complete the control tasks.
Enhanced Quality and Employee Engagement
Right first time (RFT), a metric used to track quality, is very important when the cost associated with each process is going up. Improving RFT metrics can be done with the steps outlined above in conjunction with providing ongoing staff training. For example, maximizing auto-verification rates to the ideal 92-93% in general lab reduces manual result review and errors in processing
Lab personnel that get ongoing training will also perform better. This means increased productivity and job satisfaction. Taking personnel into account in the lean framework is critical because they are the lifeblood of the lab. This will cultivate a culture of leadership and standards that propel bottom line results upwards.
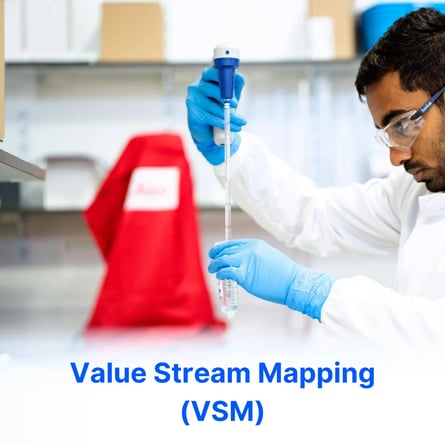
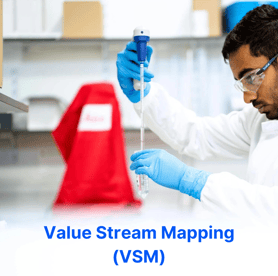
Some of these require some creative work to quantify, an example of an odd one would be a compliance rate.
A recommended way to do it, if your laboratory is subject to 100 CAP requirements (round numbers for example) and currently meets 95 of them, your compliance rate would be:
CR = (95 / 100) x 100% = 95%
Another step in the right direction is eliminating waste, or “Muda”
Muda is a Japanese term that means “waste”. It is supposed to stand for any and all activities that the business does that does not add value from the customers perspective. It had originated from the Toyota Production System by Taiichi Ohno. There were 7 forms of muda that were identified in production:
Transportation
Inventory
Motion
Waiting
Overproduction
Over-processing
Defects
All of these manufacturing wastes apply to labs, although some may be less significant than others in a lab setting and workflow. Just remember, identifying and eliminating your “muda” is still crucial for improving lab efficiency.
Strategies to eliminate “muda"
There are multiple canned strategies to eliminate waste in the lab, the first of which is the 5 S’s methodology: Sort, Set in Order, Shine, Standardize, and Sustain. It is a helpful framework for organizing your lab. The second is called “Value Stream Mapping”, it is a technique that visually represents the lab processes and can easily pin point value-adding vs. non-value-adding steps. A third step any lab can make is trying to optimizing workflows and improving inventory management. If you are a larger lab and using excel to manage inventory in fridges or shelves, it may be time to implement a different system than what you are using now. We recommend this article here[3].
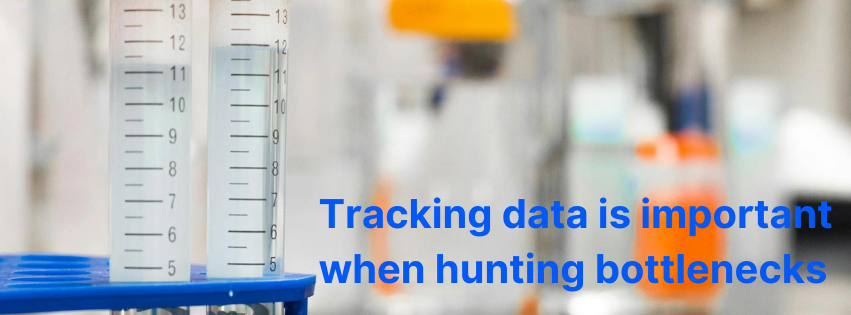
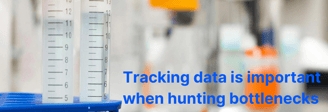
Contact Us
915 Deedra Avenue Pensacola, FL 32502 United States
(850) 696-7438
info@labqcpro.com